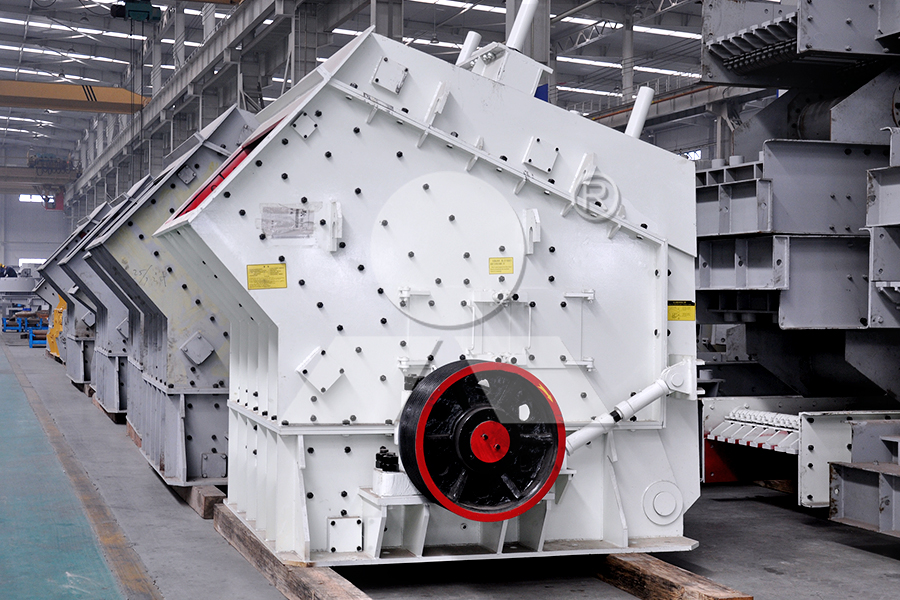
The cooperation project between Shibang Group and a steel group aims to realize the resource utilization of tailings. Tailings usually contain a lot of stone powder and mud powder, which affects the quality of sand and gravel. To this end, we chose an
The cooperation project between Shibang Group and a steel group aims to realize the resource utilization of tailings. Tailings usually contain a lot of stone powder and mud powder, which affects the quality of sand and gravel. To this end, we chose an environmentally friendly dry process and abandoned the traditional screening and washing method. This project converts raw iron tailings into high-quality sand and gravel and recyclable stone powder. The annual design treatment capacity is 7.32 million tons of waste rock, 2.81 million tons of building ballast (10-20mm), 2.39 million tons of building sand, and 2.11 million tons of reclaimed soil. In addition, after the implementation of the project, it is expected to add 2,432.02 acres of arable land. Consultation
Consultation on tailings treatment and reuse equipment
Project process and equipment configuration
In order to meet production needs, the project uses two sets of VUS450 sand and gravel co-export systems. The crushed stone is first crushed by VU impact crusher to ensure that the particle shape meets the requirements. Subsequently, the crushed stone is evenly fed into the VU model-controlled screen through the conveying equipment for classification, and the grading of the machine-made sand is accurately controlled. If there is unqualified material, it will be returned to the impact crusher for re-crushing, and the excess stone powder will be collected by the dust removal and powder collection system. The machine-made sand with reasonable grading enters the particle optimization machine for further optimization, and finally is mixed with the humidifying mixer to produce machine-made sand that meets the standards.
Processing material: gneiss
Feed particle size: 0-10mm
Output: processing capacity 270tph, finished product volume 230tph
Discharge particle size: Mx=2.8±0.2
Equipment configuration:
Two sets of VUS450 sand and gravel output system
VUS aggregate optimization system
VU impact crusher
VU mold-controlled screen
VU particle optimization machine
Customer commissioning evaluation
Before the project started, Shibang Group conducted an in-depth analysis of the raw material situation and production requirements, including production capacity, finished sand grading and investment cost. After many discussions and program reviews, a reasonable production line layout was formulated to ensure maximum benefits for customers. The VU aggregate optimization system provided is compact in design and runs smoothly, optimizing production efficiency and reducing overall operating costs.
Previous: SMP Crusher
Next: SMP Crusher
The cooperation project between Shibang Group and a steel group aims to realize the resource utilization of tailings. Tailings usually contain a lot of stone powder and mud powder, which affects the quality of sand and gravel. To this end, we chose an
The cooperation project between Shibang Group and a steel group aims to realize the resource utilization of tailings. Tailings usually contain a lot of stone powder and mud powder, which affects the quality of sand and gravel. To this end, we chose an environmentally friendly dry process and abandoned the traditional screening and washing method. This project converts raw iron tailings into high-quality sand and gravel and recyclable stone powder. The annual design treatment capacity is 7.32 million tons of waste rock, 2.81 million tons of building ballast (10-20mm), 2.39 million tons of building sand, and 2.11 million tons of reclaimed soil. In addition, after the implementation of the project, it is expected to add 2,432.02 acres of arable land. Consultation
Consultation on tailings treatment and reuse equipment
Project process and equipment configuration
In order to meet production needs, the project uses two sets of VUS450 sand and gravel co-export systems. The crushed stone is first crushed by VU impact crusher to ensure that the particle shape meets the requirements. Subsequently, the crushed stone is evenly fed into the VU model-controlled screen through the conveying equipment for classification, and the grading of the machine-made sand is accurately controlled. If there is unqualified material, it will be returned to the impact crusher for re-crushing, and the excess stone powder will be collected by the dust removal and powder collection system. The machine-made sand with reasonable grading enters the particle optimization machine for further optimization, and finally is mixed with the humidifying mixer to produce machine-made sand that meets the standards.
Processing material: gneiss
Feed particle size: 0-10mm
Output: processing capacity 270tph, finished product volume 230tph
Discharge particle size: Mx=2.8±0.2
Equipment configuration:
Two sets of VUS450 sand and gravel output system
VUS aggregate optimization system
VU impact crusher
VU mold-controlled screen
VU particle optimization machine
Customer commissioning evaluation
Before the project started, Shibang Group conducted an in-depth analysis of the raw material situation and production requirements, including production capacity, finished sand grading and investment cost. After many discussions and program reviews, a reasonable production line layout was formulated to ensure maximum benefits for customers. The VU aggregate optimization system provided is compact in design and runs smoothly, optimizing production efficiency and reducing overall operating costs.
Previous: SMP Crusher
Next: SMP Crusher