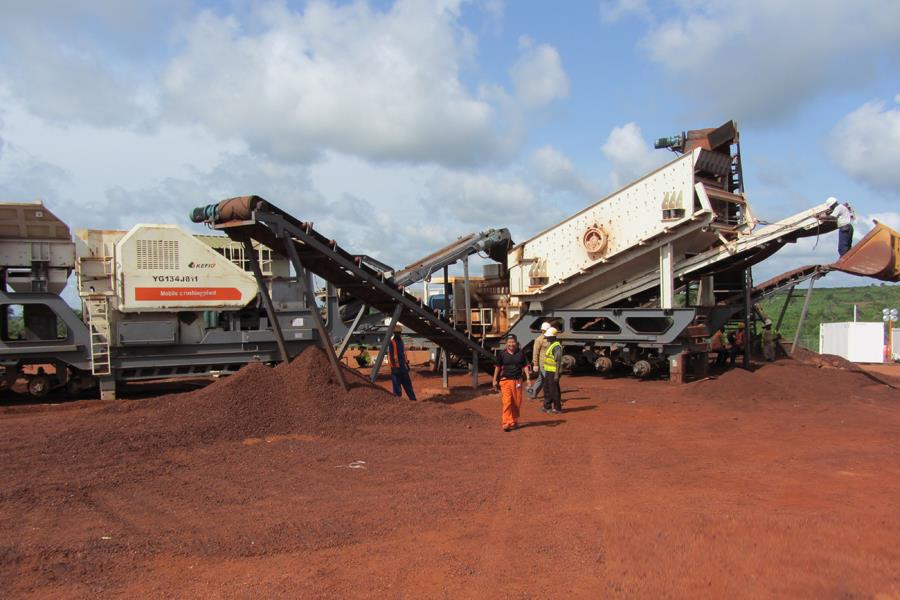
Blast furnace slag is the waste slag discharged from the production process of iron and steel plants. At present, the national iron and steel enterprises produce about 120 million tons of slag every year. Grinding slag into slag micronized powder and r
Blast furnace slag is the waste slag discharged from the production process of iron and steel plants. At present, the national iron and steel enterprises produce about 120 million tons of slag every year. Grinding slag into slag micronized powder and replacing cement with equal amount can not only turn waste into treasure, but also save mining resources needed for cement production, which is an important way to develop circular economy and realize sustainable development. Slag powder is a new type of high-strength concrete mixer, high-quality cement mixer, whose raw material is blast furnace slag of metallurgical industry, is a new environmentally friendly product using industrial waste slag. Many large iron and steel enterprises have invested in the construction of slag grinding production lines, and the slag micronized powder project is listed as a focus of the development of non-steel industry.
Slag grinding can use vertical mill, roller press, ball mill, vibrating mill and other grinding processes, or the combined grinding process of vertical mill + ball mill, roller press + ball mill, of which the vertical mill production process is more common and preferred by all steel companies. The host equipment of vertical grinding process is vertical mill and bag filter. With the progress of domestic vertical mill technology, gradually overcome its deficiencies of high vibration and easy material wear, domestic vertical mill is gradually used for the production of slag micro powder. The end equipment of the slag grinding system is the bag-type dust collector. Bag filter has the dual function of collecting finished products and environmental protection dust removal, and plays a vital role in the grinding system.
At present, the company produces slag micro powder with a specific surface area controlled between 420 and 450m2/kg. In order to ensure the fineness of the slag powder and the need for energy saving and emission reduction, the slag grinding system mainly uses the vertical grinding process. Compared with other processes, the vertical grinding process has the advantages of significant energy saving, good baking effect, small footprint and saving civil construction investment.
The equipment used in the slag powder system are: feeding equipment, hot air supply system, vertical mill, material collection equipment (dust collector). Since the vertical mill is equipped with powder selecting device inside, no external powder selecting machine is needed, which makes the vertical mill process simple.
The process flow is briefly described as follows: the raw material slag of the plant is conveyed by bucket elevator to the slag bin for storage through the feed hopper, and the bin is equipped with a spiral gate and a speed-controlled electronic belt scale to control the amount of slag in the mill, and the electronic belt scale unloads a certain amount of slag according to the needs of the system, which is fed into the vertical mill through the bucket elevator and the lock wind feeder after the iron removal by the iron remover, The powder is crushed and ground into powder by the relative movement of the grinding rollers and the grinding disc. The qualified powder is taken out of the mill with the airflow inside the mill and collected by the high concentration bag filter as the finished product, while the coarse particles fall onto the grinding plate for further grinding. The hot air inside the mill is generated by a special hot air furnace, which can be coal-fired or oil-fired according to the plant conditions, to evaporate the moisture carried by the raw material and ensure the moisture content of the product is below 1%. In order to improve the grinding efficiency of the vertical mill, on the basis of the internal circulation of powder selection in the mill, the process arrangement adopts the design that the coarse slag spit out by the mill can be returned by the system equipment, i.e. the coarse slag spit out by the mill is removed by the iron remover and then transported back to the human mill elevator by the belt conveyor, which can improve the grinding efficiency and prolong the life of the grinding rollers and grinding disc by adjusting the amount of coarse slag returned. The finished slag powder collected by the dust collector is sent to the powder storage through the conveying inclined chute.
If you are interested in our products or have questions, welcome to call our telephone +86-19937863975 or click "Business" online consultation, our customer service staff will provide you with detailed answers, thoughtful service, your satisfaction will be our unremitting impetus to move forward, welcome your click consultation.
Previous: SMP Crusher
Next: SMP Crusher
Blast furnace slag is the waste slag discharged from the production process of iron and steel plants. At present, the national iron and steel enterprises produce about 120 million tons of slag every year. Grinding slag into slag micronized powder and r
Blast furnace slag is the waste slag discharged from the production process of iron and steel plants. At present, the national iron and steel enterprises produce about 120 million tons of slag every year. Grinding slag into slag micronized powder and replacing cement with equal amount can not only turn waste into treasure, but also save mining resources needed for cement production, which is an important way to develop circular economy and realize sustainable development. Slag powder is a new type of high-strength concrete mixer, high-quality cement mixer, whose raw material is blast furnace slag of metallurgical industry, is a new environmentally friendly product using industrial waste slag. Many large iron and steel enterprises have invested in the construction of slag grinding production lines, and the slag micronized powder project is listed as a focus of the development of non-steel industry.
Slag grinding can use vertical mill, roller press, ball mill, vibrating mill and other grinding processes, or the combined grinding process of vertical mill + ball mill, roller press + ball mill, of which the vertical mill production process is more common and preferred by all steel companies. The host equipment of vertical grinding process is vertical mill and bag filter. With the progress of domestic vertical mill technology, gradually overcome its deficiencies of high vibration and easy material wear, domestic vertical mill is gradually used for the production of slag micro powder. The end equipment of the slag grinding system is the bag-type dust collector. Bag filter has the dual function of collecting finished products and environmental protection dust removal, and plays a vital role in the grinding system.
At present, the company produces slag micro powder with a specific surface area controlled between 420 and 450m2/kg. In order to ensure the fineness of the slag powder and the need for energy saving and emission reduction, the slag grinding system mainly uses the vertical grinding process. Compared with other processes, the vertical grinding process has the advantages of significant energy saving, good baking effect, small footprint and saving civil construction investment.
The equipment used in the slag powder system are: feeding equipment, hot air supply system, vertical mill, material collection equipment (dust collector). Since the vertical mill is equipped with powder selecting device inside, no external powder selecting machine is needed, which makes the vertical mill process simple.
The process flow is briefly described as follows: the raw material slag of the plant is conveyed by bucket elevator to the slag bin for storage through the feed hopper, and the bin is equipped with a spiral gate and a speed-controlled electronic belt scale to control the amount of slag in the mill, and the electronic belt scale unloads a certain amount of slag according to the needs of the system, which is fed into the vertical mill through the bucket elevator and the lock wind feeder after the iron removal by the iron remover, The powder is crushed and ground into powder by the relative movement of the grinding rollers and the grinding disc. The qualified powder is taken out of the mill with the airflow inside the mill and collected by the high concentration bag filter as the finished product, while the coarse particles fall onto the grinding plate for further grinding. The hot air inside the mill is generated by a special hot air furnace, which can be coal-fired or oil-fired according to the plant conditions, to evaporate the moisture carried by the raw material and ensure the moisture content of the product is below 1%. In order to improve the grinding efficiency of the vertical mill, on the basis of the internal circulation of powder selection in the mill, the process arrangement adopts the design that the coarse slag spit out by the mill can be returned by the system equipment, i.e. the coarse slag spit out by the mill is removed by the iron remover and then transported back to the human mill elevator by the belt conveyor, which can improve the grinding efficiency and prolong the life of the grinding rollers and grinding disc by adjusting the amount of coarse slag returned. The finished slag powder collected by the dust collector is sent to the powder storage through the conveying inclined chute.
If you are interested in our products or have questions, welcome to call our telephone +86-19937863975 or click "Business" online consultation, our customer service staff will provide you with detailed answers, thoughtful service, your satisfaction will be our unremitting impetus to move forward, welcome your click consultation.
Previous: SMP Crusher
Next: SMP Crusher