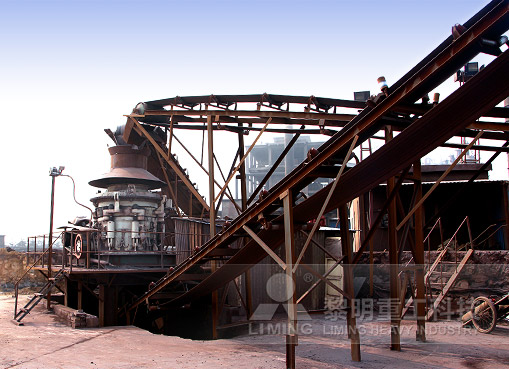
The sand making line uses 0-10mm limestone as raw material to produce 0-0.075mm stone powder and 0.075-5mm fine machine-made sand, which is mainly used for high-standard concrete materials in high-speed projects. The core equipment is the VU120 aggrega
The sand making line uses 0-10mm limestone as raw material to produce 0-0.075mm stone powder and 0.075-5mm fine machine-made sand, which is mainly used for high-standard concrete materials in high-speed projects. The core equipment is the VU120 aggregate optimization system, which combines advanced process flow to ensure the high quality and high stability of the finished sand.
Click here to consult the tower sand making construction plan
Process flow
1. Crushing stage
The raw limestone is crushed by the VU impact crusher to eliminate needle-like materials and remove sharp edges in the sand particles, so that the particle shape meets the standard requirements.
2. Grading and optimization
The crushed materials are evenly transported to the mold-controlled screen by the conveying equipment for grading and screening. Unqualified materials are returned to the impact crusher for re-crushing, and the excess stone powder is collected by the dust removal and powder collection system to ensure the accurate grading of the machine-made sand.
3. Humidification treatment
Qualified finished sand enters the humidification mixer (optional) to control the moisture content of the finished sand and further improve the quality of the finished sand.
4. Stone powder collection and packaging
The excess stone powder generated during the production process is collected by the pulse dust collector, transported to the finished material tank through the pneumatic conveying system, and packaged and transported through the packaging system.
Project advantages
1. The finished sand and gravel are of higher quality
The VU series tower sand making system adopts grinding technology and waterfall shaping technology to make the finished sand and gravel grading reasonable and the grain shape round, effectively reducing the specific surface area and porosity of the aggregate. At the same time, the dry powder removal technology makes the powder content of the finished sand adjustable and controllable to meet the sand demand of high-standard concrete.
2. High degree of automation
The supporting central control system can monitor and adjust the operating parameters of all equipment in real time to ensure the stable operation of the production line, while ensuring the high quality and high production capacity of the finished sand and gravel.
3. Green and environmental protection
The fully enclosed production design and negative pressure dust removal technology ensure that there is no sewage, sludge, and dust emission during the production process, and the noise control is also in full compliance with national environmental protection standards to achieve green production.
4. Compact structure, saving floor space
The intensive tower design greatly reduces the equipment footprint and optimizes the overall layout of the project, which is especially suitable for projects with limited space.
5. Digital processing ensures product quality
Shibang Group has an advanced CNC machine tool production line. From steel plate cutting to painting, each process is digitally controlled to ensure the high precision and reliability of the equipment, providing customers with stable and efficient production guarantees.
Previous: SMP Crusher
Next: SMP Crusher
The sand making line uses 0-10mm limestone as raw material to produce 0-0.075mm stone powder and 0.075-5mm fine machine-made sand, which is mainly used for high-standard concrete materials in high-speed projects. The core equipment is the VU120 aggrega
The sand making line uses 0-10mm limestone as raw material to produce 0-0.075mm stone powder and 0.075-5mm fine machine-made sand, which is mainly used for high-standard concrete materials in high-speed projects. The core equipment is the VU120 aggregate optimization system, which combines advanced process flow to ensure the high quality and high stability of the finished sand.
Click here to consult the tower sand making construction plan
Process flow
1. Crushing stage
The raw limestone is crushed by the VU impact crusher to eliminate needle-like materials and remove sharp edges in the sand particles, so that the particle shape meets the standard requirements.
2. Grading and optimization
The crushed materials are evenly transported to the mold-controlled screen by the conveying equipment for grading and screening. Unqualified materials are returned to the impact crusher for re-crushing, and the excess stone powder is collected by the dust removal and powder collection system to ensure the accurate grading of the machine-made sand.
3. Humidification treatment
Qualified finished sand enters the humidification mixer (optional) to control the moisture content of the finished sand and further improve the quality of the finished sand.
4. Stone powder collection and packaging
The excess stone powder generated during the production process is collected by the pulse dust collector, transported to the finished material tank through the pneumatic conveying system, and packaged and transported through the packaging system.
Project advantages
1. The finished sand and gravel are of higher quality
The VU series tower sand making system adopts grinding technology and waterfall shaping technology to make the finished sand and gravel grading reasonable and the grain shape round, effectively reducing the specific surface area and porosity of the aggregate. At the same time, the dry powder removal technology makes the powder content of the finished sand adjustable and controllable to meet the sand demand of high-standard concrete.
2. High degree of automation
The supporting central control system can monitor and adjust the operating parameters of all equipment in real time to ensure the stable operation of the production line, while ensuring the high quality and high production capacity of the finished sand and gravel.
3. Green and environmental protection
The fully enclosed production design and negative pressure dust removal technology ensure that there is no sewage, sludge, and dust emission during the production process, and the noise control is also in full compliance with national environmental protection standards to achieve green production.
4. Compact structure, saving floor space
The intensive tower design greatly reduces the equipment footprint and optimizes the overall layout of the project, which is especially suitable for projects with limited space.
5. Digital processing ensures product quality
Shibang Group has an advanced CNC machine tool production line. From steel plate cutting to painting, each process is digitally controlled to ensure the high precision and reliability of the equipment, providing customers with stable and efficient production guarantees.
Previous: SMP Crusher
Next: SMP Crusher