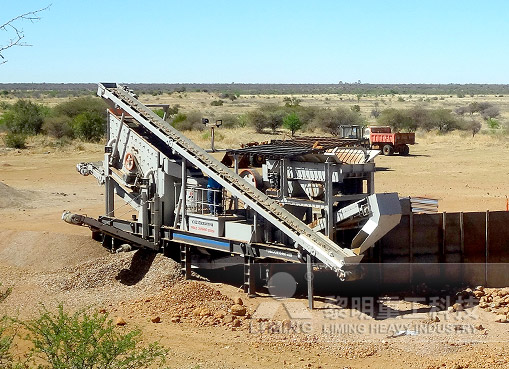
The following are the methods to reduce the wear of crushing equipment:Click here to learn about crushing equipment1. Control the coarse crushing particle size and iron inclusionThe coarse crushi
The following are the methods to reduce the wear of crushing equipment:
Click here to learn about crushing equipment
1. Control the coarse crushing particle size and iron inclusion
The coarse crushing generally uses a jaw crusher or a gyratory cone crusher (the cone crusher is usually used as the secondary equipment of the crushing production line. It can crush granite, limestone, gypsum and other rocks very well). Before the raw ore is put into the crushing, it should generally be crushed and the particle size should not exceed 600mm. In this way, in order to effectively control this particle size, a 600mmx600mm grid screen is installed at the crushing entrance for effective control. Controlling the particle size will reduce the bearing capacity of the jaw crusher, which can effectively protect the jaw plate and prevent the crushing truck.
Generally, an iron remover is installed at the jaw crusher discharge port to prevent the mining of hard iron tools such as rods and shovel teeth from entering the medium crushing, because the medium crushing equipment and liner are more than 5 times that of the coarse crushing. At the same time, the jaw crusher eats coarse and discharges coarse, which has little effect on the liner, but it is still necessary for someone to guard and pick up iron at the crusher discharge port. Ensure that the belt cleaner of the crusher scrapes the material cleanly.
2. Increase the slope of the buffer bin and material transportation channel
The factors affecting the friction coefficient of the crusher are generally: material properties, speed and temperature, load, vibration and finish. Among them, we can change the material and load. As long as we change the slope of the buffer bin or material transportation channel and increase the inclination angle 9 to reduce the positive pressure, the friction f=tg9 will be reduced in disguise, which can reduce the wear of the metal wall and increase the service life. However, this needs to be modified when conditions permit.
3. Nail a layer of polyurethane board on the metal wall through which the material passes to increase the service life of the metal wall
In the case that the buffer slope of the crusher cannot be adjusted, in addition to increasing the hardness of the steel plate, we can nail a layer of 20mm thick polyurethane protective board on the bin wall. "Hardness has a greater impact on the friction coefficient of polyurethane elastomer. Generally, the lower the hardness, the higher the friction coefficient." The smoother the surface, the smaller the friction. Because the iron ore has a high hardness, the polyurethane surface is smooth and elastic, which can effectively protect the buffer bin wall and reduce damage.
Previous: SMP Crusher
Next: SMP Crusher
The following are the methods to reduce the wear of crushing equipment:Click here to learn about crushing equipment1. Control the coarse crushing particle size and iron inclusionThe coarse crushi
The following are the methods to reduce the wear of crushing equipment:
Click here to learn about crushing equipment
1. Control the coarse crushing particle size and iron inclusion
The coarse crushing generally uses a jaw crusher or a gyratory cone crusher (the cone crusher is usually used as the secondary equipment of the crushing production line. It can crush granite, limestone, gypsum and other rocks very well). Before the raw ore is put into the crushing, it should generally be crushed and the particle size should not exceed 600mm. In this way, in order to effectively control this particle size, a 600mmx600mm grid screen is installed at the crushing entrance for effective control. Controlling the particle size will reduce the bearing capacity of the jaw crusher, which can effectively protect the jaw plate and prevent the crushing truck.
Generally, an iron remover is installed at the jaw crusher discharge port to prevent the mining of hard iron tools such as rods and shovel teeth from entering the medium crushing, because the medium crushing equipment and liner are more than 5 times that of the coarse crushing. At the same time, the jaw crusher eats coarse and discharges coarse, which has little effect on the liner, but it is still necessary for someone to guard and pick up iron at the crusher discharge port. Ensure that the belt cleaner of the crusher scrapes the material cleanly.
2. Increase the slope of the buffer bin and material transportation channel
The factors affecting the friction coefficient of the crusher are generally: material properties, speed and temperature, load, vibration and finish. Among them, we can change the material and load. As long as we change the slope of the buffer bin or material transportation channel and increase the inclination angle 9 to reduce the positive pressure, the friction f=tg9 will be reduced in disguise, which can reduce the wear of the metal wall and increase the service life. However, this needs to be modified when conditions permit.
3. Nail a layer of polyurethane board on the metal wall through which the material passes to increase the service life of the metal wall
In the case that the buffer slope of the crusher cannot be adjusted, in addition to increasing the hardness of the steel plate, we can nail a layer of 20mm thick polyurethane protective board on the bin wall. "Hardness has a greater impact on the friction coefficient of polyurethane elastomer. Generally, the lower the hardness, the higher the friction coefficient." The smoother the surface, the smaller the friction. Because the iron ore has a high hardness, the polyurethane surface is smooth and elastic, which can effectively protect the buffer bin wall and reduce damage.
Previous: SMP Crusher
Next: SMP Crusher