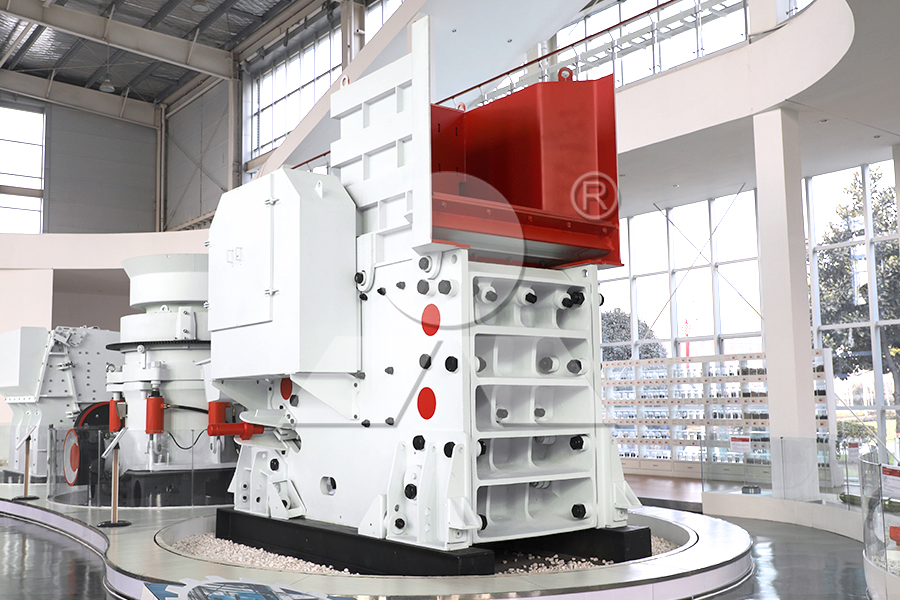
Ballast is the basic material of railway roadbed. It is made of granite and basalt and processed by crushing, screening and other processes. The configuration of equipment such as jaw crusher, cone crusher and vibrating screen is key. Ballast is widely
Ballast is the basic material of railway roadbed. It is made of granite and basalt and processed by crushing, screening and other processes. The configuration of equipment such as jaw crusher, cone crusher and vibrating screen is key. Ballast is widely used in railway construction to ensure the stability and service life of the line. Ballastless track has become a new trend, and ballast is still important.
In railway and highway construction, the stones laid on the track are called ballast. As the basic material of the roadbed, it plays an important role in support, buffering and drainage. Unlike ordinary stone, ballast must meet strict material requirements and processing standards to effectively support the stability and durability of the railway. This article will explain in detail the material selection of ballast, the configuration of the crushing production line and its application.
Introduction to ballast crushing and processing equipment
1. Material selection of ballast
Ballast is usually made of two rock materials: granite and basalt. These two stones have excellent physical properties to ensure the stability and durability of railway ballast.
Granite: As an acidic magmatic rock, granite is hard, with a Mohs hardness of 5-7, corrosion resistance, oxidation resistance, excellent elasticity and drainage performance, and is suitable as a basic material for railway roadbeds.
Basalt: This basic volcanic rock also has a Mohs hardness of 5-7, high compressive strength, good wear resistance, low crushing value, and strong asphalt adhesion, which is suitable for railway ballast stones that require higher bearing capacity.
Not only that, the quality standard of ballast stones requires that its surface must be a crushed surface, and it needs to be strictly screened and processed to ensure the cleanliness of the particles and meet specific technical indicators, such as needle index, flake index, etc.
2. Equipment configuration of ballast stone crushing production line
In order to produce ballast stones that meet quality standards, a series of processing processes such as crushing and screening must be carried out. The following are the main equipment configurations of the ballast stone crushing production line:
1. Jaw crusher (coarse crushing)
As the first process in the crushing production line, the jaw crusher is responsible for the coarse crushing of large pieces of materials and is widely used in stones with a compressive strength of no more than 320MPa. Its production capacity can range from 1t/h to 1000t/h to meet different production needs. Through the design of the "V"-shaped crushing chamber, the jaw crusher can efficiently complete the crushing of materials, and key components such as jaw plates and lining plates are made of wear-resistant alloy materials to ensure the high durability of the equipment.
2. Cone crusher (secondary crushing)
The cone crusher adopts the principle of laminated crushing and is particularly suitable for medium and fine crushing of high-hardness materials. The stone it produces has uniform particle size and strong compressive resistance, and the equipment is equipped with wear-resistant parts inside, which greatly extends the service life of the equipment. The cone crusher is suitable for further refining the coarsely crushed materials to meet the particle size requirements of ballast stones.
3. Vibrating screen (screening)
The crushed materials need to be screened by a vibrating screen to ensure that the crushed stones that meet the specifications can be effectively separated. Commonly used vibrating screen equipment includes S5X vibrating screen, Y series vibrating screen, etc., which are widely used in mining, construction and other industries. Vibrating screen can accurately screen materials of different particle sizes, improve production efficiency, and reduce materials that do not meet the standards.
4. Belt conveyor (conveying)
In the crushing and screening process, the transportation of materials is also crucial. As a basic conveying equipment, the belt conveyor has the advantages of large conveying capacity, simple structure, and convenient maintenance. It can efficiently and stably transfer materials from one process to the next.
3. Ballast stone processing process
The processing process of ballast stone generally includes the following steps:
Raw material preparation: First, the mined ore will be preliminarily screened to ensure that it meets the quality requirements of ballast stone.
Coarse crushing stage: Use a jaw crusher for coarse crushing to process large pieces of material to a particle size suitable for medium crushing.
Secondary crushing stage: Use cone crusher to further refine the coarsely crushed materials to ensure uniform particles.
Screening stage: Use vibrating screen to screen the materials and separate qualified ballast stones.
Finished product transportation: Qualified ballast stones are sent to the finished product storage area by belt conveyor and are ready to be put into use.
4. Application and importance of ballast stones
Ballast stones are widely used in railway, subway and highway construction, especially in the construction of railway ballasted tracks, playing an important role. It can not only effectively withstand the impact of trains, but also has drainage function to prevent moisture from accumulating under the roadbed, ensuring the stability and service life of the railway line.
Ballasted track: This track system uses loose granular ballast as the foundation, which is easy to lay and inexpensive, but easy to deform and requires frequent maintenance.
Ballastless track: Using materials such as concrete or asphalt as the foundation, it avoids ballast splashing, has better stability and durability, and has lower maintenance costs.
In modern railway construction, with the advancement of technology, ballastless track has gradually become a new trend, but ballast stone still plays an indispensable role in railway construction in many regions.
Previous: SMP Crusher
Next: SMP Crusher
Ballast is the basic material of railway roadbed. It is made of granite and basalt and processed by crushing, screening and other processes. The configuration of equipment such as jaw crusher, cone crusher and vibrating screen is key. Ballast is widely
Ballast is the basic material of railway roadbed. It is made of granite and basalt and processed by crushing, screening and other processes. The configuration of equipment such as jaw crusher, cone crusher and vibrating screen is key. Ballast is widely used in railway construction to ensure the stability and service life of the line. Ballastless track has become a new trend, and ballast is still important.
In railway and highway construction, the stones laid on the track are called ballast. As the basic material of the roadbed, it plays an important role in support, buffering and drainage. Unlike ordinary stone, ballast must meet strict material requirements and processing standards to effectively support the stability and durability of the railway. This article will explain in detail the material selection of ballast, the configuration of the crushing production line and its application.
Introduction to ballast crushing and processing equipment
1. Material selection of ballast
Ballast is usually made of two rock materials: granite and basalt. These two stones have excellent physical properties to ensure the stability and durability of railway ballast.
Granite: As an acidic magmatic rock, granite is hard, with a Mohs hardness of 5-7, corrosion resistance, oxidation resistance, excellent elasticity and drainage performance, and is suitable as a basic material for railway roadbeds.
Basalt: This basic volcanic rock also has a Mohs hardness of 5-7, high compressive strength, good wear resistance, low crushing value, and strong asphalt adhesion, which is suitable for railway ballast stones that require higher bearing capacity.
Not only that, the quality standard of ballast stones requires that its surface must be a crushed surface, and it needs to be strictly screened and processed to ensure the cleanliness of the particles and meet specific technical indicators, such as needle index, flake index, etc.
2. Equipment configuration of ballast stone crushing production line
In order to produce ballast stones that meet quality standards, a series of processing processes such as crushing and screening must be carried out. The following are the main equipment configurations of the ballast stone crushing production line:
1. Jaw crusher (coarse crushing)
As the first process in the crushing production line, the jaw crusher is responsible for the coarse crushing of large pieces of materials and is widely used in stones with a compressive strength of no more than 320MPa. Its production capacity can range from 1t/h to 1000t/h to meet different production needs. Through the design of the "V"-shaped crushing chamber, the jaw crusher can efficiently complete the crushing of materials, and key components such as jaw plates and lining plates are made of wear-resistant alloy materials to ensure the high durability of the equipment.
2. Cone crusher (secondary crushing)
The cone crusher adopts the principle of laminated crushing and is particularly suitable for medium and fine crushing of high-hardness materials. The stone it produces has uniform particle size and strong compressive resistance, and the equipment is equipped with wear-resistant parts inside, which greatly extends the service life of the equipment. The cone crusher is suitable for further refining the coarsely crushed materials to meet the particle size requirements of ballast stones.
3. Vibrating screen (screening)
The crushed materials need to be screened by a vibrating screen to ensure that the crushed stones that meet the specifications can be effectively separated. Commonly used vibrating screen equipment includes S5X vibrating screen, Y series vibrating screen, etc., which are widely used in mining, construction and other industries. Vibrating screen can accurately screen materials of different particle sizes, improve production efficiency, and reduce materials that do not meet the standards.
4. Belt conveyor (conveying)
In the crushing and screening process, the transportation of materials is also crucial. As a basic conveying equipment, the belt conveyor has the advantages of large conveying capacity, simple structure, and convenient maintenance. It can efficiently and stably transfer materials from one process to the next.
3. Ballast stone processing process
The processing process of ballast stone generally includes the following steps:
Raw material preparation: First, the mined ore will be preliminarily screened to ensure that it meets the quality requirements of ballast stone.
Coarse crushing stage: Use a jaw crusher for coarse crushing to process large pieces of material to a particle size suitable for medium crushing.
Secondary crushing stage: Use cone crusher to further refine the coarsely crushed materials to ensure uniform particles.
Screening stage: Use vibrating screen to screen the materials and separate qualified ballast stones.
Finished product transportation: Qualified ballast stones are sent to the finished product storage area by belt conveyor and are ready to be put into use.
4. Application and importance of ballast stones
Ballast stones are widely used in railway, subway and highway construction, especially in the construction of railway ballasted tracks, playing an important role. It can not only effectively withstand the impact of trains, but also has drainage function to prevent moisture from accumulating under the roadbed, ensuring the stability and service life of the railway line.
Ballasted track: This track system uses loose granular ballast as the foundation, which is easy to lay and inexpensive, but easy to deform and requires frequent maintenance.
Ballastless track: Using materials such as concrete or asphalt as the foundation, it avoids ballast splashing, has better stability and durability, and has lower maintenance costs.
In modern railway construction, with the advancement of technology, ballastless track has gradually become a new trend, but ballast stone still plays an indispensable role in railway construction in many regions.
Previous: SMP Crusher
Next: SMP Crusher