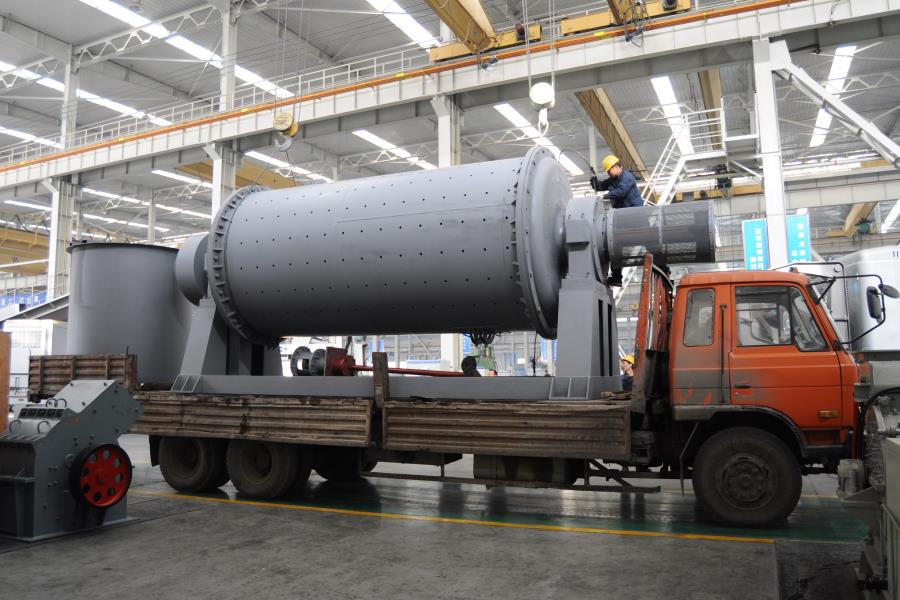
For the dryer that often handles corrosive materials, we must do a good job of anti-corrosion. Usually, the dryer consists of support system, cylinder and welded parts, and there are different anti-corrosion methods for different parts and uses of the
For the dryer that often handles corrosive materials, we must do a good job of anti-corrosion. Usually, the dryer consists of support system, cylinder and welded parts, and there are different anti-corrosion methods for different parts and uses of the dryer. There are three main anti-corrosion methods commonly used:
Dryer
Electrostatic powder coating method
The electrostatic powder coating method is a method of applying new powder coatings to new powder coatings.
Many manufacturers use the old method of spraying liquid paints, but these liquid paints contain a lot of organic solvents such as esters and ketones and hydrocarbons, which are flammable, explosive and unsafe, causing a lot of trouble in production, construction, storage and transportation, and these liquids are usually toxic and evaporate into the air, which can cause serious pollution to the environment.
When we manufacture dryers, we usually use cold rolled stainless steel, which is very costly, instead of ordinary carbon steel. The corrosion resistance of the powder coating used in the electrostatic powder coating method is exactly equal to that of stainless steel, and we can use ordinary carbon steel instead of stainless steel.
This powder coating has the characteristics of toughness, durability, good decorative properties, excellent outdoor weathering and heat resistance, as well as excellent resistance to industrial dryer corrosion and chalking resistance, excellent gloss and color performance, can completely replace the use of stainless steel dryer.
In addition, this powder coating has toughness, durability, good decorative features, excellent outdoor weathering and heat resistance, while having excellent industrial dryer corrosion resistance, excellent gloss and color light to replace the stainless steel dryer.
Welds are welded with austenitic nickel-chromium stainless steel
Many parts of the dryer must be welded, and the materials used in old welds often break and corrode. It has a serious impact on the service life of the dryer. The difference between austenitic nickel-chromium stainless steel and ordinary carbon steel lies in the poor thermal conductivity, large coefficient of thermal expansion and high resistance value. These characteristics limit this material in welding must use special methods. However, this steel has high corrosion resistance.
Passivation, phosphating method
In the manufacture and production of dryers, many parts use carbon steel. If the working time is long, it is easy to cause a lot of rust on its surface, which often requires a lot of manual rust removal. Passivation and phosphating method is mainly through electrochemical reaction and one-time treatment, which can not only make the surface of the rusty steel workpiece show the original color of the metal, but also produce a dense anti-rust film layer on the metal surface. After using this method, even if we put the equipment in a humid environment, it will not rust. Moreover, this method is extremely simple, which can save a lot of labor and material resources, reduce investment, and is a widely used anti-corrosion method.
Previous: SMP Crusher
Next: SMP Crusher
For the dryer that often handles corrosive materials, we must do a good job of anti-corrosion. Usually, the dryer consists of support system, cylinder and welded parts, and there are different anti-corrosion methods for different parts and uses of the
For the dryer that often handles corrosive materials, we must do a good job of anti-corrosion. Usually, the dryer consists of support system, cylinder and welded parts, and there are different anti-corrosion methods for different parts and uses of the dryer. There are three main anti-corrosion methods commonly used:
Dryer
Electrostatic powder coating method
The electrostatic powder coating method is a method of applying new powder coatings to new powder coatings.
Many manufacturers use the old method of spraying liquid paints, but these liquid paints contain a lot of organic solvents such as esters and ketones and hydrocarbons, which are flammable, explosive and unsafe, causing a lot of trouble in production, construction, storage and transportation, and these liquids are usually toxic and evaporate into the air, which can cause serious pollution to the environment.
When we manufacture dryers, we usually use cold rolled stainless steel, which is very costly, instead of ordinary carbon steel. The corrosion resistance of the powder coating used in the electrostatic powder coating method is exactly equal to that of stainless steel, and we can use ordinary carbon steel instead of stainless steel.
This powder coating has the characteristics of toughness, durability, good decorative properties, excellent outdoor weathering and heat resistance, as well as excellent resistance to industrial dryer corrosion and chalking resistance, excellent gloss and color performance, can completely replace the use of stainless steel dryer.
In addition, this powder coating has toughness, durability, good decorative features, excellent outdoor weathering and heat resistance, while having excellent industrial dryer corrosion resistance, excellent gloss and color light to replace the stainless steel dryer.
Welds are welded with austenitic nickel-chromium stainless steel
Many parts of the dryer must be welded, and the materials used in old welds often break and corrode. It has a serious impact on the service life of the dryer. The difference between austenitic nickel-chromium stainless steel and ordinary carbon steel lies in the poor thermal conductivity, large coefficient of thermal expansion and high resistance value. These characteristics limit this material in welding must use special methods. However, this steel has high corrosion resistance.
Passivation, phosphating method
In the manufacture and production of dryers, many parts use carbon steel. If the working time is long, it is easy to cause a lot of rust on its surface, which often requires a lot of manual rust removal. Passivation and phosphating method is mainly through electrochemical reaction and one-time treatment, which can not only make the surface of the rusty steel workpiece show the original color of the metal, but also produce a dense anti-rust film layer on the metal surface. After using this method, even if we put the equipment in a humid environment, it will not rust. Moreover, this method is extremely simple, which can save a lot of labor and material resources, reduce investment, and is a widely used anti-corrosion method.
Previous: SMP Crusher
Next: SMP Crusher