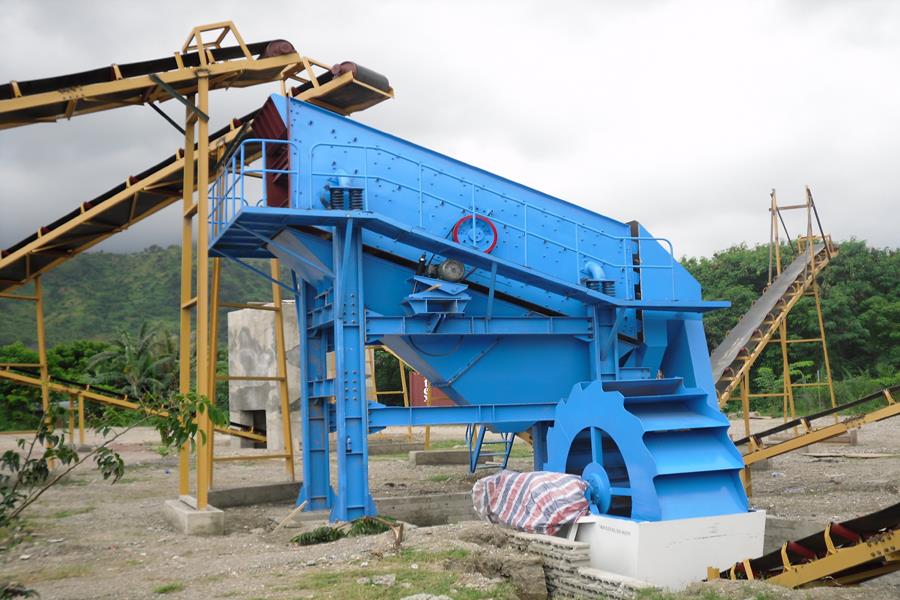
With the increase in railway infrastructure, the demand for ballast stone has increased. Granite and basalt are the main choices. Shibang Group equipment crushing and screening, C6X jaw crusher, HST cone crusher and other combinations are recommended.
With the increase in railway infrastructure, the demand for ballast stone has increased. Granite and basalt are the main choices. Shibang Group equipment crushing and screening, C6X jaw crusher, HST cone crusher and other combinations are recommended. The ballast stone production line has achieved remarkable results, is environmentally friendly and efficient, and meets the high-quality needs of railways.
In recent years, with the continuous advancement of infrastructure projects, the demand for ballast gravel in railway construction has increased year by year. Especially in Guangdong Province's transportation "14th Five-Year Plan", there are a considerable number of railway construction projects, and the demand for ballast stone is also growing rapidly. So, what kind of stone is used for railway ballast stone? What about its production process?
Recommendation of railway ballast crushing and sand making equipment
1. Types and requirements of railway ballast stone
Railway ballast refers to the gravel layer laid under the railway track. Its main functions include carrying and dispersing the weight of the train, reducing vibration and noise, drainage and supporting sleepers, etc. In order to meet the high standards of railway operation, ballast stone must have high hardness, good pressure resistance and low water absorption. Therefore, granite and basalt became the main choices:
Granite: has a dense structure, hard texture, strong wear resistance and weathering resistance, and is elastic, which is beneficial to track bed drainage.
Basalt: has high hardness, wear resistance, corrosion resistance and strong pressure resistance. It is an excellent railway ballast material and is suitable for long-term outdoor use.
2. Production process flow of ballast stone
The production of ballast stone generally uses excavated rocks for crushing and screening to form granular gravel that meets railway material standards. In order to achieve stable production, efficient equipment such as jaw crushers, cone crushers, and vibrating screens provided by Shibang Group are usually used.
Ballast production process flow:
Coarse crushing stage: Large stones enter the jaw crusher through the vibrating feeder for preliminary coarse crushing. The deep V-shaped crushing cavity design of the jaw crusher can improve production efficiency and reduce material blockage.
Secondary crushing stage: The coarsely crushed materials enter the cone crusher and are further processed into secondary crushed stone. The cone crusher uses a hydraulic motor to adjust the discharge port to facilitate control of the discharge particle size, and wear-resistant parts extend the service life of the equipment.
Screening and transportation: The crushed stone processed by the cone crusher is then screened by the vibrating screen. The particles larger than the set specifications are returned to the cone crusher for re-crushing to form the final ballast stone product.
3. Recommendation of core equipment
In order to meet the high strength demand of railway ballast stone, Shibang Group recommends the following equipment combination:
C6X series jaw crusher: suitable for coarse crushing of large stones. It is made of high-hardness materials and has stable performance.
HST single-cylinder hydraulic cone crusher: laminated crushing, suitable for medium crushing of high-hardness stone, with high degree of automation.
VSI6X sand making machine: used for the production of high-quality machine-made sand, adapting to a variety of aggregate needs.
K series mobile crushing station: a project suitable for the flexible needs of the site, easy to move and adjust the site.
4. Application and effects of ballast stone production projects
In multiple railway infrastructure projects, this ballast stone production line solution has achieved remarkable results. The finished product has excellent grain shape and reasonable gradation, and has been widely recognized by the market. The ballast production based on environmental protection not only meets the construction needs, but also provides high-quality stone support for railway projects, achieving a win-win situation of economic and environmental benefits.
Previous: SMP Crusher
Next: SMP Crusher
With the increase in railway infrastructure, the demand for ballast stone has increased. Granite and basalt are the main choices. Shibang Group equipment crushing and screening, C6X jaw crusher, HST cone crusher and other combinations are recommended.
With the increase in railway infrastructure, the demand for ballast stone has increased. Granite and basalt are the main choices. Shibang Group equipment crushing and screening, C6X jaw crusher, HST cone crusher and other combinations are recommended. The ballast stone production line has achieved remarkable results, is environmentally friendly and efficient, and meets the high-quality needs of railways.
In recent years, with the continuous advancement of infrastructure projects, the demand for ballast gravel in railway construction has increased year by year. Especially in Guangdong Province's transportation "14th Five-Year Plan", there are a considerable number of railway construction projects, and the demand for ballast stone is also growing rapidly. So, what kind of stone is used for railway ballast stone? What about its production process?
Recommendation of railway ballast crushing and sand making equipment
1. Types and requirements of railway ballast stone
Railway ballast refers to the gravel layer laid under the railway track. Its main functions include carrying and dispersing the weight of the train, reducing vibration and noise, drainage and supporting sleepers, etc. In order to meet the high standards of railway operation, ballast stone must have high hardness, good pressure resistance and low water absorption. Therefore, granite and basalt became the main choices:
Granite: has a dense structure, hard texture, strong wear resistance and weathering resistance, and is elastic, which is beneficial to track bed drainage.
Basalt: has high hardness, wear resistance, corrosion resistance and strong pressure resistance. It is an excellent railway ballast material and is suitable for long-term outdoor use.
2. Production process flow of ballast stone
The production of ballast stone generally uses excavated rocks for crushing and screening to form granular gravel that meets railway material standards. In order to achieve stable production, efficient equipment such as jaw crushers, cone crushers, and vibrating screens provided by Shibang Group are usually used.
Ballast production process flow:
Coarse crushing stage: Large stones enter the jaw crusher through the vibrating feeder for preliminary coarse crushing. The deep V-shaped crushing cavity design of the jaw crusher can improve production efficiency and reduce material blockage.
Secondary crushing stage: The coarsely crushed materials enter the cone crusher and are further processed into secondary crushed stone. The cone crusher uses a hydraulic motor to adjust the discharge port to facilitate control of the discharge particle size, and wear-resistant parts extend the service life of the equipment.
Screening and transportation: The crushed stone processed by the cone crusher is then screened by the vibrating screen. The particles larger than the set specifications are returned to the cone crusher for re-crushing to form the final ballast stone product.
3. Recommendation of core equipment
In order to meet the high strength demand of railway ballast stone, Shibang Group recommends the following equipment combination:
C6X series jaw crusher: suitable for coarse crushing of large stones. It is made of high-hardness materials and has stable performance.
HST single-cylinder hydraulic cone crusher: laminated crushing, suitable for medium crushing of high-hardness stone, with high degree of automation.
VSI6X sand making machine: used for the production of high-quality machine-made sand, adapting to a variety of aggregate needs.
K series mobile crushing station: a project suitable for the flexible needs of the site, easy to move and adjust the site.
4. Application and effects of ballast stone production projects
In multiple railway infrastructure projects, this ballast stone production line solution has achieved remarkable results. The finished product has excellent grain shape and reasonable gradation, and has been widely recognized by the market. The ballast production based on environmental protection not only meets the construction needs, but also provides high-quality stone support for railway projects, achieving a win-win situation of economic and environmental benefits.
Previous: SMP Crusher
Next: SMP Crusher